Welcome to the comprehensive guide on Reciprocating Compressors. In this article, we will delve deep into the working principle, various components, and provide you with a detailed buyer’s guide. Whether you’re an industry professional seeking a refresher or a novice looking to make an informed purchase, you’re in the right place.
Understanding Reciprocating Compressors
Reciprocating Compressors play a pivotal role in various industrial applications, thanks to their efficient mechanism. Let’s explore the working principle and key components that make these compressors tick.
Working Principle
Reciprocating compressors operate on a straightforward principle. They use a piston within a cylinder to compress gas, which is then discharged into a storage tank. This process occurs in two phases: compression and discharge. During compression, the piston moves upward, reducing the cylinder’s volume and increasing pressure. Subsequently, during discharge, the compressed gas is expelled into the storage tank.
Essential Parts
To fully grasp the functionality of reciprocating compressors, it’s crucial to understand their components. Here are the key parts:
1. Cylinder
The cylinder is the heart of the compressor, where the compression and discharge phases take place. It must be sturdy and heat-resistant to endure high-pressure conditions.
2. Piston
The piston is a crucial moving part that creates the compression effect. It moves up and down within the cylinder, generating the necessary pressure to compress the gas.
3. Valves
Reciprocating compressors have two sets of valves: inlet and discharge. Inlet valves allow gas into the cylinder during the suction phase, while discharge valves facilitate the expulsion of compressed gas during the discharge phase.
4. Crankshaft
The crankshaft connects the piston to the motor, translating rotary motion into reciprocating motion.
5. Motor
The motor provides the necessary power to drive the compressor, ensuring consistent operation.
6. Cooling System
To prevent overheating, reciprocating compressors are equipped with cooling systems that dissipate heat generated during compression.
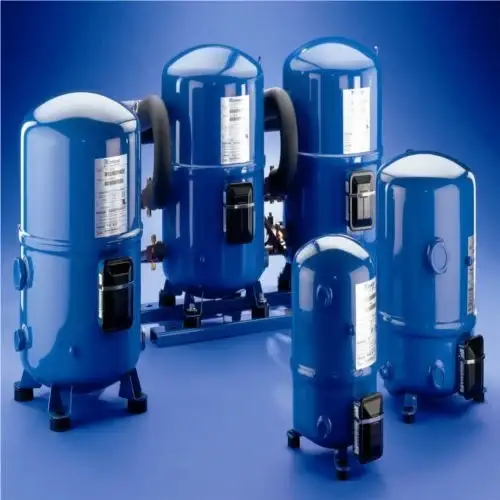
Reciprocating Compressors: Buyer’s Guide
When it comes to purchasing a reciprocating compressor, several factors need consideration. Making the right choice can significantly impact your operations and productivity.
1. Capacity and Pressure Requirements
Determine the specific needs of your application, including the required capacity (measured in cubic feet per minute, CFM) and operating pressure (measured in pounds per square inch, PSI). Ensure the compressor you choose meets or exceeds these requirements.
2. Single-Stage vs. Two-Stage
Consider the compressor’s stage configuration. Single-stage compressors are suitable for lower pressure applications, while two-stage compressors are ideal for high-pressure needs.
3. Power Source
Reciprocating compressors can be electrically powered or run on gasoline or diesel. Choose a power source that aligns with your facility’s infrastructure and requirements.
4. Size and Portability
Evaluate the available space and mobility needs. Determine whether a stationary or portable compressor best suits your workspace.
5. Maintenance
Factor in the ease of maintenance. Look for models with accessible components and a reputation for durability.
6. Noise Levels
Consider noise pollution in your workspace. Select a compressor with sound-dampening features if noise is a concern.
Conclusion
In conclusion, understanding the working principle and components of reciprocating compressors is vital for making an informed purchase decision. By following our buyer’s guide and considering key factors, you can select the perfect compressor for your specific needs. Whether it’s for industrial processes or DIY projects, the right reciprocating compressor can enhance efficiency and productivity.
FAQs
How does a reciprocating compressor differ from a rotary compressor?
Reciprocating compressors use a piston-cylinder mechanism for compression, while rotary compressors employ rotating blades or screws. Reciprocating compressors are typically more suitable for high-pressure applications.
What lubrication is required for reciprocating compressors?
Reciprocating compressors require proper lubrication to reduce friction and heat. Oil-lubricated compressors are common and need regular oil checks and changes.
Can reciprocating compressors handle continuous operation?
Yes, reciprocating compressors are capable of continuous operation, provided they are adequately maintained and meet the workload requirements.
Are there energy-efficient reciprocating compressors available?
Yes, energy-efficient models with variable-speed drives are available, helping you save on electricity costs.
What safety precautions should be taken when operating reciprocating compressors?
Ensure proper ventilation to prevent heat buildup, perform regular maintenance checks, and follow safety protocols when working with compressed gases.
How long do reciprocating compressors typically last?
The lifespan of a reciprocating compressor depends on factors such as maintenance and usage. Well-maintained compressors can last 10-15 years or more.