Centrifugal pumps are a fundamental piece of machinery in various industries, from water supply to chemical processing. Understanding their components, working principles, types, and applications is crucial for engineers, operators, and anyone interested in fluid dynamics. In this article, we’ll delve deep into the world of centrifugal pumps, shedding light on their intricate workings and diverse applications.
Key Components
Impeller
The heart of any centrifugal pump is the impeller. This high-speed rotating component is responsible for imparting kinetic energy to the fluid, causing it to move through the pump. Impellers come in various designs, such as open, closed, and semi-open, each tailored for specific applications.
Casing
The casing houses the impeller and guides the flow of fluid. It is designed to maximize the efficiency of the pump and direct the fluid in the desired direction. Casings can be volute, vortex, or axial flow, depending on the pump’s purpose.
Shaft
The shaft connects the impeller to the motor, transmitting rotational energy. It must be sturdy and precisely aligned to ensure smooth operation. Materials like stainless steel or carbon steel are commonly used due to their strength and corrosion resistance.
Bearings
Bearings support the shaft and reduce friction. Proper lubrication and maintenance of bearings are essential to prevent wear and tear, which can lead to pump failure.
Working Principle
Centrifugal pumps work on the principle of centrifugal force. When the impeller rotates, it creates a low-pressure area at the center, causing fluid to be drawn into the pump’s inlet. As the fluid moves outward toward the casing, it gains velocity and pressure. Finally, it’s discharged through the outlet at a higher pressure, ready for various applications.
Types of Centrifugal Pumps
Single-Stage vs. Multi-Stage
Centrifugal pumps can be single-stage or multi-stage. Single-stage pumps have a single impeller and are suitable for low to moderate pressure applications. Multi-stage pumps, on the other hand, feature multiple impellers in series and are capable of handling high-pressure tasks.
Radial Flow vs. Axial Flow
The flow direction of the fluid also categorizes centrifugal pumps. Radial flow pumps move fluid perpendicular to the impeller’s rotation, while axial flow pumps move it parallel to the impeller’s axis. The choice depends on the specific application’s requirements.
Self-Priming vs. Non-Self-Priming
Self-priming pumps have the ability to evacuate air from the suction pipe, making them ideal for applications where the pump is not continuously submerged. Non-self-priming pumps require the pump to be primed manually.
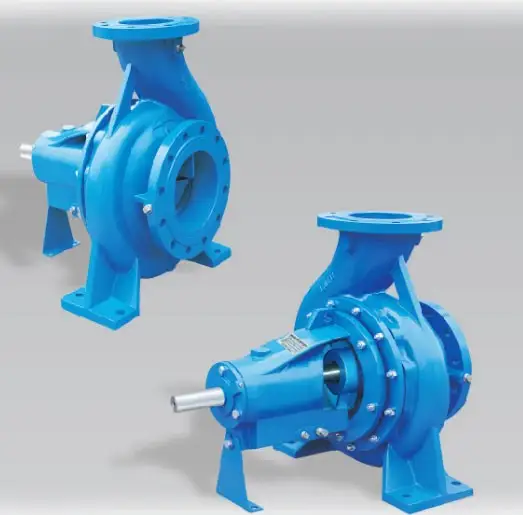
Applications
Centrifugal pumps find applications in a wide range of industries:
Water Supply
Municipalities and industries use centrifugal pumps to transport water from source to destination. Their reliability and efficiency are crucial for ensuring a steady water supply.
Chemical Processing
In chemical plants, these pumps handle the transfer of various chemicals. Material selection is critical to resist corrosion and ensure safety.
HVAC Systems
Centrifugal pumps circulate chilled or heated water in HVAC systems, regulating temperature in commercial and residential buildings.
Agriculture
For irrigation and drainage, centrifugal pumps are indispensable in agriculture. They help distribute water across vast fields efficiently.
Oil and Gas
In the oil and gas industry, centrifugal pumps are used for crude oil transportation, gas processing, and more.
Conclusion
In conclusion, centrifugal pumps play a vital role in numerous industries by efficiently moving fluids from one place to another. Understanding their components, working principles, types, and applications is crucial for optimizing their use. Whether you’re dealing with water supply, chemical processing, or HVAC systems, a well-informed approach to centrifugal pumps can lead to improved efficiency and reliability.
FAQs
Q: How does a centrifugal pump differ from a positive displacement pump? A: Unlike positive displacement pumps, which move fluid by trapping it in a chamber and pushing it out, centrifugal pumps rely on centrifugal force to accelerate fluid.
Q: Can I use a single-stage centrifugal pump for high-pressure applications? A: Single-stage pumps are best suited for low to moderate pressure tasks. For high-pressure applications, consider a multi-stage centrifugal pump.
Q: What maintenance is required for centrifugal pumps? A: Regular maintenance includes lubricating bearings, checking for leaks, and inspecting impellers for wear. It’s essential to follow the manufacturer’s recommendations.
Q: Are centrifugal pumps suitable for handling abrasive fluids? A: Centrifugal pumps may not be the best choice for highly abrasive fluids. In such cases, specialized pumps with abrasion-resistant materials are preferred.
Q: Can a centrifugal pump handle viscous liquids like honey or molasses? A: Centrifugal pumps are better suited for low-viscosity fluids. For viscous liquids, consider using a positive displacement pump.
Q: What is the role of the volute casing in a centrifugal pump? A: The volute casing helps convert kinetic energy generated by the impeller into pressure energy, ensuring efficient fluid movement.